What is Electroplating
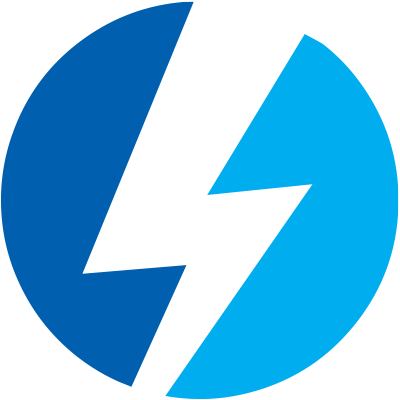
Electroplating, also known as electrodeposition, is a surface finishing technique that utilizes electricity to deposit a different metal coating on a solid metal object. For example, a silver watch can be plated in gold to give the watch the appearance that it is solid gold. Often times electroplating is used to enhance a metal item by coating it in a metal that has increased conductivity, corrosion resistance, or visual appeal.
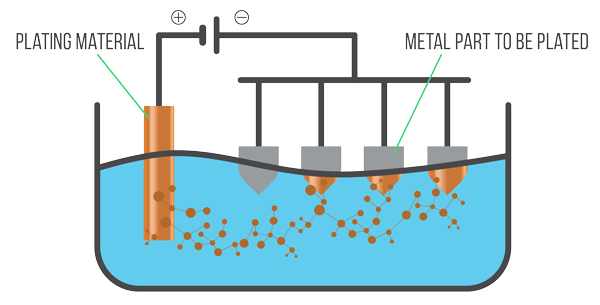
Electroplating Process
The electroplating process is typically broken into three categories: pre-treatment, treatment, and post-treatment.
Pre-treatment
During the pre-treatment stage, the part is fully prepared for treatment. This commences with disassembling any connected parts to ensure an even coat of electroplating solution can reach the entirety of the part’s surface area. Next, the part is completely stripped of any particles which can cause blisters or flakes; this includes old metal coatings, as well as, greases or dusts that are on the part. Finally, the piece is polished ensuring any imperfections on the piece are smoothed and even, additionally any remaining oxidation on the object’s surface is removed during the polishing process.
Treatment
The first step in the treatment phase begins with dipping the workpiece in a cleaning solution and electrifying it. This process allows the coating to adhere to the workpiece. The workpiece is then connected to the negative lead of a power source while the positive lead is placed directly in the plating solution. Once the power source is turned on, the metal atoms on the anode begin to oxidize and dissolve into the electrolyte solution where they adhere to the surface of the workpiece. The length of time the workpiece remains in the solution is dependent on the desired thickness. The process often takes anywhere from 5 to 45 minutes.
Post-treatment
While many jobs are completed after the product is removed from the electrolyte solution, some jobs require a bit more work. Some metal coatings requite a clear coat to further prevent tarnishing and improve corrosion resistance. Electroplating generates a hazardous waste, so recycling and proper waste removal are key to staying in line with governmental regulations.
Industries that Utilize Electroplating
Several industries are dependent on the electroplating process for specific metal coated parts used in their day to day operations. The automotive industry commonly uses zinc-nickel plating solutions to prevent corrosion in harsh environmental conditions. The aerospace and military industries both frequently use titanium plating due to its high strength to weight ratio. Gold plating is commonly used by the electronics industry due to its conductivity. The jewelry industry frequently uses gold plating as a cheaper alternative to solid gold.
Shanley pump offers GemmeCotti plastic and stainless steel magnetic drive pumps for the surface finishing industry. These pumps are designed to handle caustic chemicals used during the electroplating process. The magnetic driven impeller eliminates the need for a seal, which minimizes needed repairs, and eliminates leakage protecting your employees from dangerous liquids being used during the plating process. Give us a call or email us to see how we can assist you in all of your pumping needs.