How Microorganisms Cause Coolant to Smell Rancid
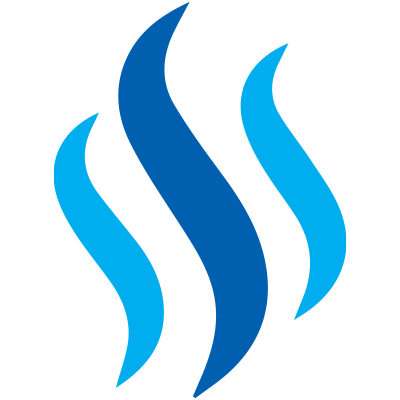
“Monday morning stench” is an expression many machine shop employees are familiar with, but not often enough is the origin of the problem realized, and even less frequently are the other consequences of this problem realized. The odor that greets machinists on a typical Monday morning is generated by microorganisms breaking down oils and reproducing within the coolant sump. The microorganisms that create the unpleasant aroma are anaerobic, which means they do not require oxygen to survive. These bacteria feed on tramp oils (hydraulic, spindle, and lubricating oils) which percolate from other components of the system. Modern machine coolant is designed to reject tramp oils, which causes them to float to the surface over time. A machine shop that operates only five days a week can create the following phenomena: Friday production has just ended, and the lights and machines are turned off for the weekend. Within the sump, tramp oils begin rising to the top of the sump, aerobic bacteria (bacteria that requires oxygen) begins multiplying. By Saturday the tramp oils have fully risen to the top, this creates a barrier at the top of the sump which denies oxygen from entering the oils. At this point the aerobic bacteria has fully depleted the sump of oxygen and begins to die, which allows the anaerobic bacteria to thrive. As the Anaerobic bacteria flourishes, they feed and breakdown the machine coolant and produce hydrogen sulfide, which produces the rotten-egg odor known as “Monday morning stench”.
The Cost of Coolant Going Bad
The odor is the effect that is first noticed by operators, but more issues are created due to the bacteria. As the bacteria feeds on the coolant, it alters the chemical makeup of the coolant, resulting in: splitting of emulsions, decreased PH, increased corrosion, and a loss of lubricating ability. The changes to the coolant will cause issues in the machining process: parts may begin to rust sooner than expected, the decrease in lubricity causes more friction, which will increase the wear on the cutting edge of tools, and the excess heat can cause the finish on the workpiece to be inadequate, resulting in further work to be done in order to smooth out the finish. Excess bacteria and fine metal particles can cause clogs in lines, filters, and valves. Lastly, well maintained coolant will last much longer; therefore, reducing the expenses associated with replacing and disposing of old dirty coolant.
In addition to the physical ramifications to the machine and work pieces caused by dirty coolant, there is also significant repercussions to employee health that machine shops should consider. Dirty coolant can induce micro-abrasions; this is caused when coolant splashes on the machine operator, and he naturally wipes it off causing the small metal particles to create miniature scratches on the skin. If there is a higher microorganism count in the coolant, this creates an increased risk of infection of these scratches. Also, some higher speed machines can cause a mist to form from the coolant, small metal particles in the mist can cause damage to lung tissue when inhaled, such as lung scarring and emphysema.
Tips to Properly Maintain Coolant
The consequences of using contaminated coolant far outweighs the costs and efforts required to properly maintain coolant. A proper system should include exceptional filtration; less fine metal particles will result in lower bacterial growth. Good housekeeping practices in general can help lower the rate at which contaminants enter the fluid, this will also benefit employee safety by providing an uncluttered work environment. Lastly, it is important to regularly remove tramp oils, metal chips, and sludge from the sump. This practice will require full removal of coolant from the sump, which will require a dependable pump. Shanley Pump is your one stop shop for pumps; Our GemmeCotti centrifugal pumps are great for emptying sump, as it can handle the alkalinity and small solids within the fluid. Shanley Pump also stocks Seim PWO pumps for high-pressure coolant applications, as well as our Edur DAF centrifugal pumps that help float solids to the surface for removal. Give us a call today to see how we can assist your Machine shop in maintaining best practices for better performance.
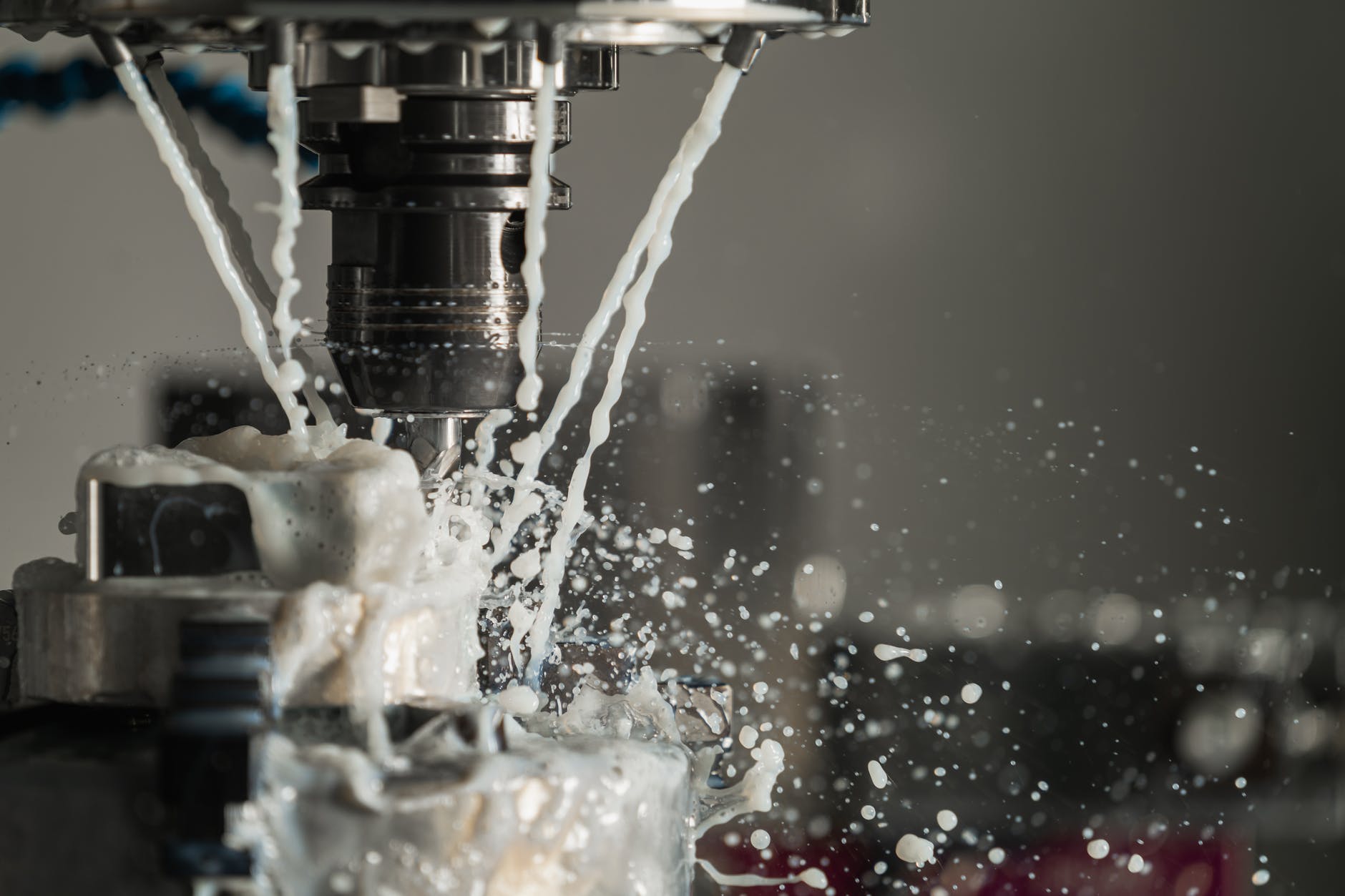