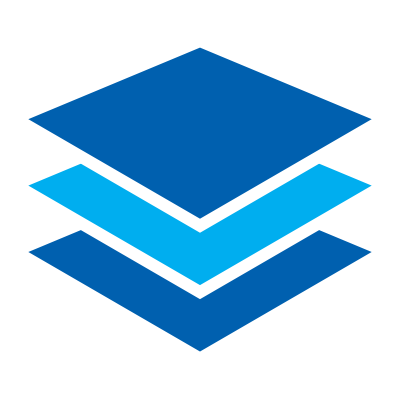
Often times when a metal piece is finished being produced, a final step is initiated that alters the surface of the metal to protect the part from corrosion or enhance the metal piece in some way; this is known as a surface finish. The three most popular surface finishes are electroplating, electropolishing, and passivation. Frequently a combination of the finishes can be used. Shanley Pump offers GemmeCotti plastic magnetic drive pumps for the surface finishing industry. These pumps are designed to handle caustic chemicals used during all three of the surface finishes mentioned above. The magnetic driven impeller eliminates the need for a seal, which minimizes needed repairs and leakage, consequently protecting your employees from dangerous liquids used during the finishing process.
Electroplating
Electroplating, also known as electrodeposition, is a surface finishing technique that utilizes electricity and an electrolytic solution to deposit a different metal coating on a solid metal object. For example, a silver watch can be plated in gold to give the appearance that it is solid gold. Often times electroplating is used to enhance a metal item by coating it in a metal that has increased conductivity, corrosion resistance, or better visual appeal.
Electropolishing
Electropolishing is ultimately the opposite of electroplating. With electropolishing electricity and an electrolytic solution are utilized to remove metal ions from a metal piece. This process is typically performed on stainless steel to completely smooth the surface and remove any embedded contaminants. The image below shows a microscopic view of a part before and after being electropolished. Electropolishing is primarily utilized by the food and pharmaceutical industry, as the perfectly smooth finish electropolishing provides allows disinfectant to easily cover the entire surface area, where small imperfections in a metal could allow bacteria to thrive.
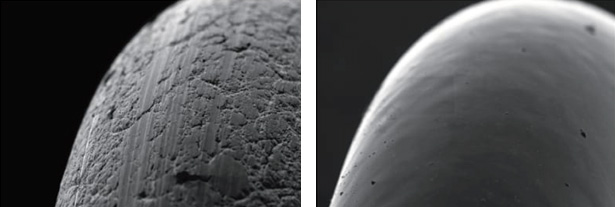
Passivation
Passivation is a metal finishing process that is primarily used on stainless steel to prevent corrosion. The process involves passing the metal piece through citric or nitic acid. This removes any iron that may be embedded within the surface from the machining process. Passivation also creates a thick oxide layer over the product, causing it to be more resistant to chemical reactions that could cause rust and other forms of corrosion.